- Цветы и растения
- Аквариум и рыбы
- Для работы
- Для сайта
- Для обучения
- Почтовые индексы Украины
- Всяко-разно
- Электронные библиотеки
- Реестры Украины
- Старинные книги о пивоварении
- Словарь старославянских слов
- Все романы Пелевина
- 50 книг для детей
- Стругацкие, сочинения в 33 томах
- Записи Леонардо да Винчи
- Биология поведения человека
Главная ![]() ![]() |
Логістика - Кальченко А. Г.
7.4. СИНХРОНІЗАЦІЯ ЦИКЛІВ ВИРОБНИЦТВА
Синхронізація циклів виготовлення виробів та їх частин є складовою будь-якого виробничого процесу, але це явище, як правило, непомітне, тобто його начебто немає. Якщо синхронізація циклів процесів некерована, тривалість циклів зростає втричі, тому що тоді календарне вирівнювання кожної частини процесу перевищить розмір найбільшого циклу відповідної частини процесу. Це справедливо для кожного рівня розподілу процесу виготовлення виробу на частини: операція, деталь, комплектооперація, комплект деталей, стадія виготовлення виробу (заготівельна, механооброблювальна, складальна). Некерована синхронізація призводить до значного перевищення раціонального рівня незавершеного виробництва та спричиняє великі втрати робочого часу робітників і обладнання (на тепер у непоточному виробництві ці втрати робочого часу сягають 50 %). Знання закону синхронізації циклів процесів виготовлення виробів та їх частин необхідні як основа мистецтва керування виробничим процесом з метою мінімізації витрат на виробництво. Для забезпечення конкурентоспроможності підприємства можливість мінімізації витрат на виробництво має, як правило, першочергове значення.
Міжопераційне пролежування предметів праці та простої робочих місць у процесі виготовлення виробів слугують своєрідними календарними компенсаторами, що вирівнюють календарну тривалість суміжних технологічних операцій на виробничих дільницях.
Календарна організація усіх форм поточного виробництва ґрунтується на принципі безперервного руху деталей: синхронізація тривалості деталеоперацій тут мала б здійснюватись тільки за рахунок простоїв робочих місць, але це не є ефективним, тому що година простою робочого місця (робітника і обладнання) коштує дорожче ніж час пролежування однієї деталі. Тому організовується паралельно-послідовний рух деталей, коли усі мікропростої робочих місць концентруються.
Концентрація стає можливою за рахунок припущення деякого міжопераційного пролежування деталей. Концентрація мікропауз простоїв кожного робочого місця дозволяє звільнити робітника і на цей час перевести його на іншу операцію. Тут синхронізація тривалості деталеоперацій щодо розміру такту поточної лінії відбувається як за рахунок простоїв обладнання робочих місць, так і за рахунок міжопераційного пролежування деталей.
За будь-якої форми організації виробництва нерівні тривалості технологічних операцій вирівнюються до деякої календарної межі або за рахунок пролежування деталей, або за рахунок простоїв робочих місць, або за рахунок того й іншого одночасно. Вирівнювання тривалості технологічних операцій у непоточному виробництві має дві об’єктивні причини. Перша полягає в тому, що за умов поточного виробництва організація безперервності протікання виробничого процесу у непоточному виробництві вимагає синхронізації тривалості операції. Друга причина вирівнювання — необхідність комплектування партій предметів праці у процесі їх виготовлення до розмірів планово-облікової одиниці (машинокомплект, умовний комплект, бригадокомплект, маршрутний комплект тощо).
Календарна межа вирівнювання тривалості технологічних операцій характеризує виробничий процес з обох його протилежних боків — як безперервність завантаження робочих місць (Rj) і як безперервність виготовлення предметів праці (Ri).
Не викликає сумнівів те, що за заданих організаційно-технологічних умов мінімум витрат на виробництво досягається при найбільшій безперервності використання засобів виробництва (робочих місць), а це відповідає єдиному оптимальному рівню виготовлення партій виробів у виробництві (Re).
Об’ємно-динамічний метод планування й організації виробництва за принципом безперервного завантаження планових робочих місць дає змогу забезпечити не тільки безперервне завантаження планових робочих місць, а й максимальну тривалість виробничого циклу створення аналізованого маршрутного комплекту деталей (TМДК). Якщо на кожній операції процесу виготовлення маршрутного комплекту деталей (тобто на комплектооперації) використовується одне чи більше робочих місць, то тривалість його виробничого циклу можна визначити за формулою:
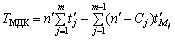
де n? — кількість найменувань виробів, що будуть виготовлені на ділянці у певному плановому періоді і складають один комплект деталей;
— середній інтервал часу, через який здійснюється передача партії виробів одного найменування на наступну комплектооперацію після завершення їх обробки на j-й комплектооперації
— менший з двох середніх інтервалів часу, через які здійснюється передача деталей комплекту з суміжних j-ї чи (j + 1)-ї комплектооперацій;
Cj — кількість робочих місць, використаних в обробці деталей комплекту на більш вузькій j-й комплектооперації;
tj — середня тривалість виконання технологічних операцій з виготовлення деталей комплекту на j-й комплектооперації (чи на
j-му рівні робіт);
j — порядковий номер комплектооперації чи операції типового технологічного маршруту, за яким деталі зазначеного комплекту проходять обробку (j = 1, m).
Тут цикл виготовлення комплекту деталей визначається з урахуванням умов організації виробничого процесу: кількості номенклатурних позицій у плані (n?); кількості робочих місць, що використовуються на кожній операції процесу (Cj); середньої тривалості виконання однієї технологічної операції з деталями комплекту на кожній j-й комплектооперації (Re). За цією формулою визначається зв’язок між кількістю номенклатурних позицій у плані, плановим строком виконання робіт і нормативним розміром партії деталей.
Календарна синхронізація циклів виготовлення деталей має явний характер. Так, якщо деталі мають однакову кількість операцій, то їх цикли вирівнюються внаслідок вирівнювання тривалості операцій з їх виготовлення. Деталі у виробничих підрозділах виготовляються, як правило, комплектами, а це означає, що тривалість циклу виготовлення кожної деталі комплекту дорівнює тривалості циклу виготовлення даного комплекту деталей.
Created/Updated: 25.05.2018